How is Edge Strength Provided in Laminated Glass Production?
How is Edge Strength Provided in Laminated Glass Production?
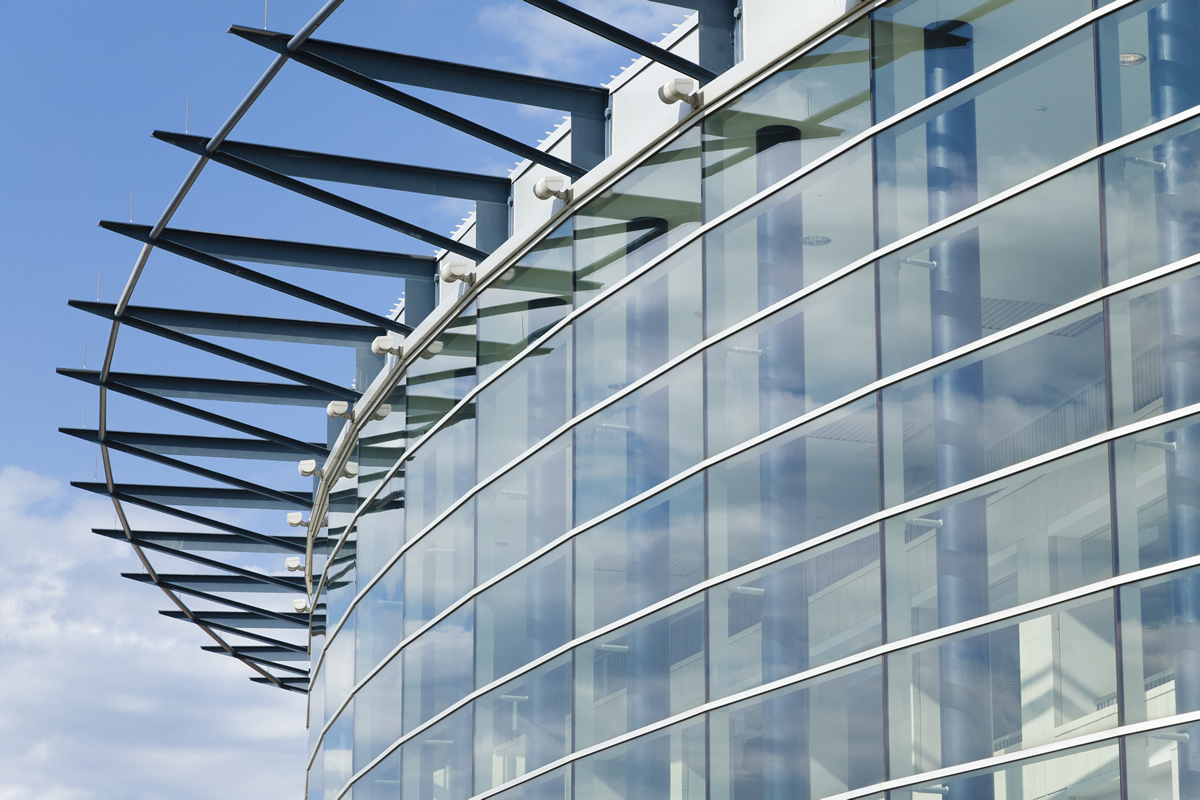
How is Edge Strength Provided in Laminated Glass Production?
The purpose of this article is to reveal the issues to be considered in the face of questions about edge strength (stability) as the use of Laminated safety glass in outdoor applications is increasingly widespread; thus, to exhibit the rules that must be followed from production to assembly stage.
DEFINITIONS AND RECIPES:
Edge Strength: The ability of the edges of laminated glass to resist discoloration, bubbling, delamination or other staining over time when exposed to environmental conditions.
Tests for Edge Strength: High Temperature Test, Condensing or Non-Condensing Humidity Tests as detailed in TS EN ISO 12543-4
The main factors affecting the edge strength are:
- Lamination process
- Application conditions
Lamination Process: The Lamination Process is roughly removing the air trapped between the glasses and the intermediate binders by means of heat and pressure and ensuring that they adhere to each other under the most optimum conditions. Throughout the process, there are several variables that play an important role in the edge strength of Laminated Glass. These variables are the adhesion of the interlayer to the glass, the quality of the glass, and finally the sealing of the edges together.
Adhesion: The adhesion of the intermediate binder to the glass plays an important role in the edge strength of the finished product. As well as the chemical structure of the material chosen as the intermediate binder, different levels of adhesion are obtained due to the different prescription of the intermediate binder with the same chemical structure.
MATTERS TO BE CONSIDERED FROM CUTTING TO THE FINAL PRODUCT:
There are many factors that can affect the level of adhesion during the lamination process. These are stated below.
The first factor is the cleanliness of the glass. When it reaches the Glass Laminate line, the cutting oil, the properties of the volatile substances in this oil, dust and other foreign substances on the surface can carry with it. The glass must be cleaned before Pre-Lamination begins. At this point, the quality of washer+dryers becomes important.
Since the cleanliness of the glass surface and the quality of the water affect the adhesion of the interlayer to the glass, it is recommended to use only demineralized, that is, pure water. Water should have a low conductivity. Water from natural or municipal sources contains dissolved salts that impart hardness to the water. These salts typically consist of Ca(Calcium), Mg(Magnesium), Na(Sodium) and K(Potassium) ions.
The first two negatively affect adhesion even at low concentrations, the second has a lower but still measurable effect. Loss of adhesion, especially at the edge, can lead to edge bubbles or delamination.
The moisture content of the intermediate layer is the second key factor for adhesion. PVB is hygroscopic (that is, it has the ability to reduce the water molecules in the environment it is in by diffusion or condensation on its wall) and its adhesion to glass is inversely proportional to its moisture content. It is produced with an optimum moisture content of around 0.4% and then the roll is hermetically sealed in a foil bag to prevent moisture absorption.
Once the foil wrap is opened, the PVB will begin to absorb moisture from the air until an equilibrium is reached. To avoid this, open PVB rolls should be stored in an environment with a relative humidity of 25-30%. It is also recommended to replace the foil packaging and close it, especially if the storage conditions are not sufficient.
Ionoplast interconnects also absorb moisture, but at a much slower rate. Since the optimum moisture content is lower than PVB, it is always recommended to reseal foil packaging unless stored in a clean room below 10% RH.
Less adhesion on the edges can result in water/moisture seepage between the layers over time, discoloration, bubbles and/or delamination.
Quality of Glass: Most of the glass used for lamination is produced by flotation process. Standard float glass, also called annealed glass, although high quality and very flat, is not considered safety glass because it breaks into large, sharp and dangerous pieces. In addition, the bending and tensile strength of annealed glass is relatively weak. For this reason, the glass is subjected to thermal strengthening treatment (heat treatment) to make it safer and stronger.
Here we come to the problem that heat-treated glass poses for Lamination. That is natural deterioration caused by heat treatment. When glass undergoes heat treatment, it begins to deform and become wavy.
This distortion causes a general or local fluctuation, edge curling. Although there have been great technological developments in tempering furnaces in recent years and the possibility of obtaining smoother glass has increased, it is always possible to create a problem for lamination. For this reason, care should be taken to use the flattest glass possible in lamination.
Even the acceptable values specified in TS EN 12150 are not strict enough for Lamination. A general rule is that the deviation of flatness should be less than 10% of the interlayer thickness. For example, the maximum flatness deviation of the tempered glass layer to be used in the production of Laminated Glass using a 0.76 mm intermediate binder should be 0.076 mm. A deviation greater than this tolerance on the edge has the potential to create bubbles or delamination.
Edge sealing: The autoclave process is the final step in the production of laminated glass. The conditions inside the autoclave allow for a viscous flow of the interlayer, thereby ensuring close contact of the intermediate binder and the glass. The intervening air is expelled and a clear, clean laminate is formed.
When placing Laminated Glass in the autoclave cart, spaces should be left between them to allow sufficient air flow to ensure uniform heating and cooling of each glass and glass layers. In addition, the windows must be firmly fixed to the autoclave trolley so that there is little movement during the autoclave cycle and the balance provided for air circulation is maintained. Moreover, excessive movement of the glasses in the autoclave may also cause glass breakage. When fixing laminated glasses, care should also be taken not to apply excessive pressure to the edges. Because excessive pressure to be applied to the edge will cause thinning of the intermediate layer at this point, disrupting the edge smoothness and may cause air bubbles or delamination in this area.
Another important point is to autoclave the glasses coming out of the pre-lamination as soon as possible and start the process. Excessive delays, especially edge adhesion, can cause poorly sealed edges to begin to separate.
The autoclave is then set to a pressure of 12-15 bar and a temperature of 135-145°C. When the upper temperature and pressure are reached, these values are maintained for at least 30 minutes. Here, the length or shortness of time depends on the glass thickness and the load size in the autoclave. After the holding time has elapsed, the glass is allowed to cool while still under pressure.
The pressure should not be relieved until the interlayer/glass temperature drops below 50°C, otherwise small bubbles may start to appear at the edges.
APPLICATION CONDITIONS:
There are various ways to install laminated glass, although different, there are some basic precautions that must be followed in all installations. These are stated below.
Contact with water: Even for glasses produced in the best lamination conditions, prolonged contact with water should not be allowed. If laminated glass is installed in a joinery, suitable channels must be provided to drain the accumulated water. For glasses with exposed edges, the smoothness of the glass, the proper cleaning of pvb wastes, etc. is important. Thus, it is ensured that there is no standing water on the edge surface.
If the point supports are not closed properly on the glasses mounted with the Spider system, water may leak into the opening and cause delamination.
Compatibility of other chemicals that may come in contact with the edge of laminated glass: This is particularly relevant for sealants and joint sealants. Mismatch of sealant and joints with the interlayer can cause edge bubbles, discoloration or delamination. It is therefore necessary to test for compatibility.
There are various sealants on the market. While compatible with most ionoplast laminates, laminated glass using pvb may experience some minor edge blemishes. It is best to contact the sealant or interlayer manufacturer to determine compatibility.
The final potential cause of edge stains is the environmental conditions in which the laminated glass is installed and the level of conformity of the chemical content of the intermediate binder to these environmental requirements. Is laminated glass indoors or outdoors? In a dry environment or in a wet environment? Is it near the seaside or the ocean? Is PVB used or ionoplast used? Based on these answers, different levels of edge strength can be obtained.
IN CONCLUSION: There is no standard laminated production condition, or choice of a standard intermediate binder type or thickness. We cannot talk about a Laminated Glass suitable for all conditions. For this reason, choices should be made by reviewing a number of conditions described above, from production to environmental conditions. Otherwise, it will be difficult for us to encounter defects and even to understand what causes them.