Laminated Glass Control
Laminated Glass Control
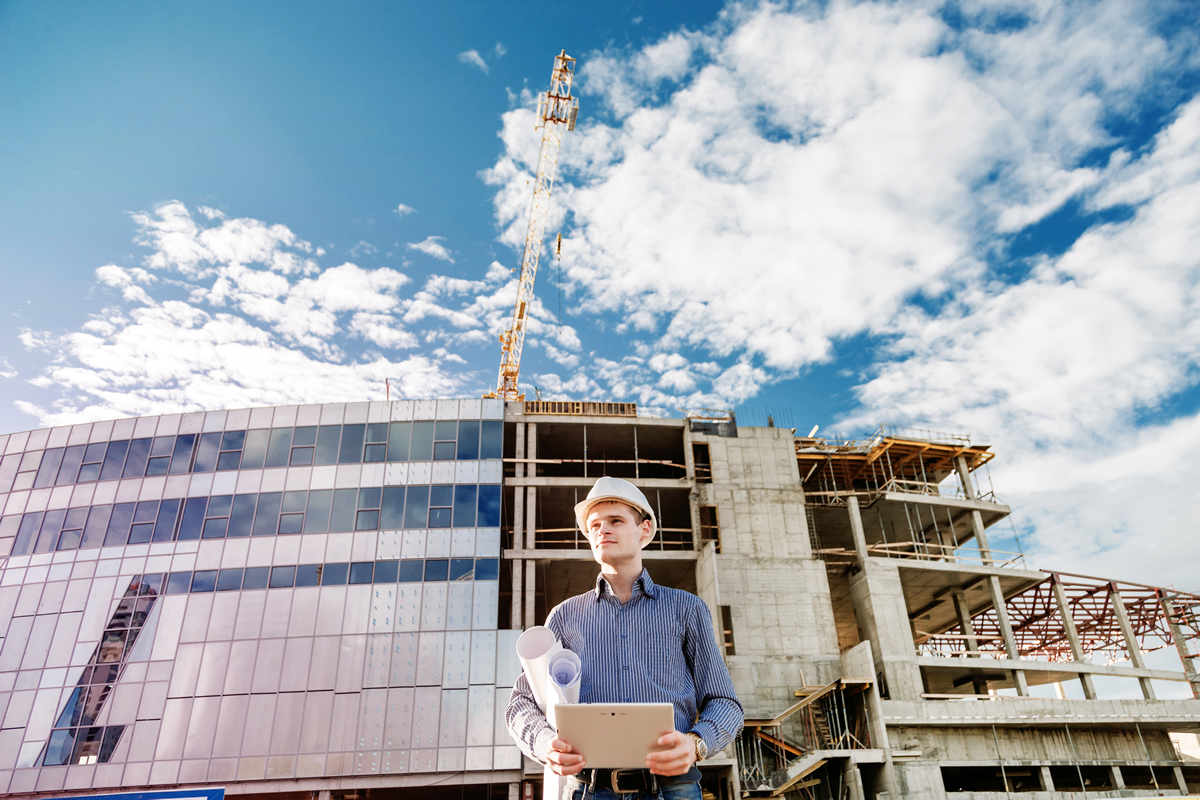
14 FACTORS THAT SHOULD BE CONSIDERED BY COMPANIES PURCHASING LAMINATED GLASS
POINTS TO BE CONSIDERED IN CONTROL OF FINAL PRODUCT INPUT
1. Is there a slightly hazy appearance or haze in one area and a clear view in the other? If it does, that means the pvb quality is low. It was probably produced by adding waste pvb. Or an error has occurred in the process. In both cases, the adhesion level of pvb to glass is low. It carries the possibility of delamination in the future.
2. Is there any yellowing in the appearance of the glass? If so, there could be two main reasons for this. Either the pvb is of poor quality or the glass autoclave has been given multiple times or the process value has been determined at high temperature. You have the right to return the glass.
3. There should be no air bubbles smaller than the size of a pinhead but forming a clump in the glass gap. If so, it is a process defect. These blisters can multiply and expand in moist, wet environments.
4. Are there air bubbles in perforated spider laminated glasses, especially around the edges of the holes? Even if these bubbles are to be closed by the puncture apparatus, there is a risk of them growing and being exposed in the future.
5. Is there fluctuation in optical appearance along the edge region, around the hole or gouge? If there are, this means that large air bubbles were formed during the production process, these areas were clamped with a vise to correct these defects and the glass was autoclaved a second time.
6. Is there any pvb run-out on the edges? If any, these areas may cause accumulation in contact with water or moisture, you may encounter delamination starting from these areas in the future.
7. Are there any sharp-edged slits or cracks that extend from the edge of the glass to the inside of the piece? If there is, this defect is non-standard. You can request a return of the glass.
8. Inside the glass – not in the intermediate space – air bubbles, bubbles, buttons, etc., originating from raw materials. Is there any fault? If there are any, it is an acceptable defect if they are at most 1 per m2. If there is more than that, the glass is of poor quality. You need to check the terms of the contract. If a condition is not put forward about the origin of the glass, it is inevitable that you will encounter these and similar defects.
9. No foreign matter, hair, feathers, stains, dust, etc. between the two glasses. There should be no foreign matter. There should be no scratches in the form of scrapes on the inner or outer surface of the glass.
The image should not be wrinkled. These are all manufacturing faults.
10. If there is a vein-shaped appearance defect in the glass image, this is not an acceptable defect. It is a defect caused by the poor quality and inhomogeneity of the intermediate binder pvb.
11. When you control the measurement;
a. The total thickness of the laminated glass is ± 0.2 mm for each glass thickness. Tolerances in the interlayer film thickness are not taken into account.
b. The offset tolerance is acceptable within the limits shown in the table below.
Offset is the misalignment that occurs at any edge of the glass sheet component or clear plastic sheet. The boat may not be the same in width or height of the glass. The largest outboard will be considered.
If the width or length is less than or equal to 1 m, the offset tolerance is 2 mm.
If the width or length is between 1 and 2 m, the offset tolerance is 3 mm.
If the width or length is between 2 and 4 m, the offset tolerance is 4 mm.
If the width or length is greater than 4 m, the offset tolerance is 6 mm.
12. According to the types of defects, the acceptability tolerances in the field of view are as follows.
Point defects in the field of view: Such defects include opaque spots (visible defects such as inclusions or traces of tin in the glass or interlayer), blebs or foreign matter. Defects smaller than 0.5 mm in diameter are not taken into account. Large defects greater than 3 mm are not allowed. This situation is explained in the table below.
If four or more defects are at a distance of less than 200 mm from each other, this indicates an accumulation of defects. This distance is reduced to 180 mm for laminated glass consisting of three sheets, to 160 mm for laminated glass consisting of four sheets, and to 150 mm for laminated glass consisting of five or more sheets. You can find the details of these in the TS EN ISO 12543-5 standard.
13. You must have requested a running-in process on laminated glasses whose edges do not go into the frame. The processing must be run-on. However, running-in should not be done after the laminate process. Some companies require lapping after lamination to remove the unsightly appearance caused by the appearance of pvb between two glasses or slips between two glass plates. Some glass processing companies also accept this in the name of "customer satisfaction". However, laminated glass, which will be used especially in outdoor environments, will be subjected to thermal shock as it will be exposed to temperature differences, which will increase the stress on the tempered glass as it is run in after temper + laminated glass, and as a result, the risk of glass explosion will increase.
14. In addition, during the running-in process after laminate, the pvb between the two glasses will be exposed to a tension-tension tendency, pvb will be able to run away from the edge, at least the stickiness value of pvb will decrease. This may cause pvb to be exposed to moisture more than other glasses and cause image defects and color changes, which we call blooming at the edges.